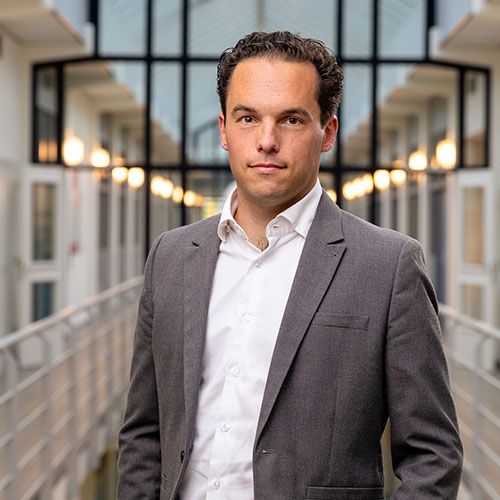
Generate near-infinite permutations of complex, domain-specific, 3D environments
Unscheduled maintenance and machine breakdown are significant costs during a system’s life cycle. While preventive maintenance can be costly, breakdowns and downtime are often more expensive, affect customer satisfaction and imply risks due to machine failures.
We optimize your machine operation quality by monitoring your machine’s health and the application of smart algorithms for predictive maintenance. Predictive maintenance is a balance between preventive and reactive maintenance which optimizes costs against the safer and optimal error-free operation of the device.
Optimizing machine operation quality goes further than just predictive maintenance, and can also involve the use of smart (auto) calibration of your system’s components. With machine learning techniques like time series analysis and anomaly detection, we are able to continuously monitor your system’s health, ensuring optimal operation of the device, and decrease in the cost of ownership and customer satisfaction.
Generate near-infinite permutations of complex, domain-specific, 3D environments
Increase functionality by actionable knowledge extraction
More robust machine vision applications
Optime control and machine performance